医药厂房施工的关键在于洁净系统,其施工技术的质量直接影响着产品质量的好坏,关系国民生命健康安全。在洁净系统的构建操作中的核心为洁净工艺管道施工技术,我们在要保证每一个环节的规范性,及时发现潜在问题,杜绝质量通病,最大程度的消除施工隐患。
一、洁净管道施工环境要求
洁净管道的材料放置和管道预制、焊接,必须设置符合规范要求的专用场所。洁净管道施工对施工环境的要求有:(1)材料预制场和预制品存放库应清洁、卫生,安装前材料必须包装密封完好;(2)卫生级管道配管作业与非不锈钢安装作业不得再同一区域同时进行;(3)在安装作业期间,安装区域每日清洁1~2次,保证施工环境的清洁;(4)严禁将碳钢类材料和附有油脂类机具带入洁净预制场所和现场清洁室;(5)进入现场洁净室,必须穿无尘清洁工作服装。
二、洁净管道的安装
(1)材料检查
管道安装施工前,首先应对管道、管件和密封件等进行仔细检查。所有材料必须要有出厂格书和材质证明书。管道、管件、阀门、法兰等材质、外径与壁厚必须符合设计和规范要求。焊接前先将管道及管件等施焊材料在盛有CCL4的液体池浸泡15min以上,再将其清水冲洗2~3遍,最后用干毛巾擦干,去除自带的油脂及杂质,保证焊接质量。
(2)管道加工
管道应按照施工现场的实际位置认真核实后方可下料,还应当充分考虑减少焊口数量。在切割管道时一般不宜采用润滑剂,注意保证管道切口平直光滑,不得有毛刺、裂纹、缩孔、氧化物、夹渣等现象。
(3)管道焊接
管道施工过程中,需按照施工图纸结合施工工艺及现场实际情况进行优化设计,避免无谓的转弯,变径,减少卫生死角。当管道穿越洁净区与非洁净区时,管子外壁和建筑隔断之间会产生空隙,必须对空隙进行有效密封。
①点焊。在正式焊接前都需采用手动方式对焊缝进行点焊。焊点沿焊缝外圆均匀分布。点焊点位厚度宜均匀且薄。
②充氩。管道点焊作业完成后,用卡盘和卡箍固定好其余接口,用端盖将管道密封并充气,当检测管段中含氧量小于0.1%~1%时即可。充氩保护是洁净管道焊接最重要的步骤之一,无氩或缺氩保护的情况下,会造成管道内壁焊缝发黑、焊缝外观不规则。
③焊接。管道焊接是洁净管道安装施工的最重要一环,管道焊接的质量除受上述相关因素的影响外还与焊接条件、人员素质及其他因素有关。例如:电压、电流波动,焊接作业人员的作业熟练程度等。手工焊时,拉弧的距离以及焊针的研磨及环境温湿度、风速都可能影响焊缝质量。目前,常用的自动焊机是焊针围绕母材旋转焊接。焊针在升降焊接过程中,材料上下温度不同,有可能导致管道内壁焊缝产生层状堆积,因此焊接时要注意焊机电流和速度。
④保温。药厂洁净管道保温一般采用硅酸盐和珍珠岩。在洁净室明装区域外常采用硅酸盐外包铝皮。在洁净区内,一般采用不锈钢套管内充珍珠岩。
(4)阀门、法兰的安装
阀门、法兰与管道的连接不允许错位安装,错位会产生凹槽型卫生死角而导致微生物滋生。现阶段的卫生级洁净管道与阀门的连接方式大量采用卡箍卡盘连接方式,便于拆卸,且减少污染死角。
(5)管架安装
管道支架的预制和安装也应尽可能地考虑避免积液或积尘,最好选用不锈钢成品支撑架,支架表面应光洁便于手工清洁。同时,管架的安装还要充分考虑介质的流向,保证管线的坡度符合规范要求,防止洁净管道系统内出现积液现象而滋生细菌。
三、药厂洁净管道检验及系统试验
(1)打码及照片
洁净管道施工完成后,根据要求不同,需对全自动焊点进行激光打码编号,10%~20%的自动焊焊口进行内窥镜检查照片。
(2)管道清洗及酸洗钝化
在配管完成后,为了去除管线内的表面油脂、焊缝氧化物、游离铁离子等污物,需要对洁净不锈钢管进行酸洗钝化。
(3)系统试验与调试
工程竣工验收前,需要对整个洁净管道系统进行调试。调试前,还需要进行管道压力试验。洁净管道系统水压试验多采用纯化水为试验用水,试验压力为1.5倍工作压力;管道气压试验采用洁净氮气作为试验用气,试验压力为1.25倍工作压力。
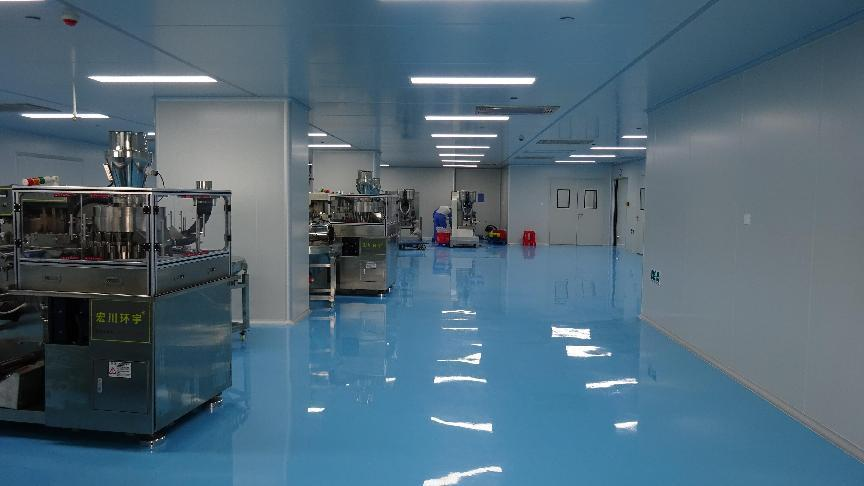
广东赛特净化设备有限公司工程项目服务范围:洁净车间、无尘车间、药厂生产车间、药厂洁净车间、药厂GMP车间、保健品洁净车间、保健品无尘车间、保健品GMP车间、干细胞实验室、冻干粉针剂洁净车间、冻干粉针剂无尘车间、手术室、PCR实验室、口罩洁净车间、口罩生产车间、医疗器械无尘车间、医疗器械洁净车间、印刷车间、微生物实验室、胶体金生产车间、胶体金洁净车间、胶囊洁净车间、胶囊无尘车间、GMP车间、实验室、电子厂洁净车间、电子厂无尘车间、百级生产车间、二极管洁净车间、二极管无尘车间、电子材料洁净车间、电子材料无尘车间、锂电池车间、锂电池洁净车间、锂电池无尘车间、光学材料无尘车间、光学材料洁净车间、光学材料生产车间、单晶硅洁净车间、单晶硅无尘生产车间、试剂室、大输液洁净车间、针剂洁净车间、生物实验室、食品厂洁净车间、食品厂无尘车间、压片糖洁净车间、压片糖无尘车间、奶粉洁净车间、奶粉生产车间、奶粉无尘车间。